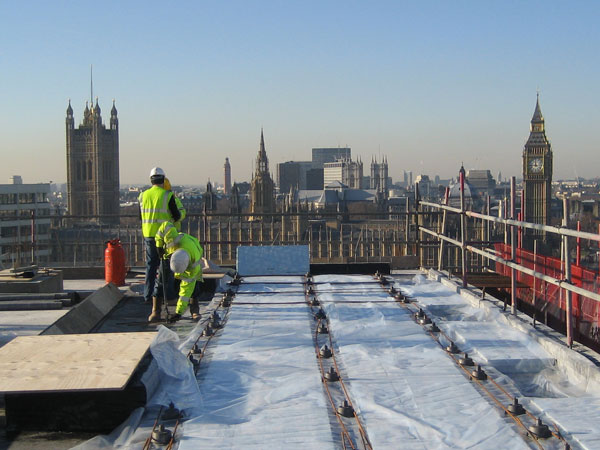
Installation of Floating Floors
Mason U.K. Ltd will design, supply and install our jack up floating floor system including the supply and finish of the concrete.
All of our Project Engineers have the relevant CSCS cards and CITB Supervisor Accreditation necessary for site work. Risk assessments and method statements are undertaken for every project. We can supply a full turn-key solution, including:
� Design of the floor layout and slab reinforcing, allowing for any wall or equipment loads
� Supply of all necessary aspects including steel, labour and concrete
� Complete installation including concreting
� Concrete finishing as required
� Jacking the floor to the required datum, leaving the floor ready for other trades.
Time Lapse Footage of Installations
This video includes a time-lapse capture showing the jacking of one of many floors for a recording studio and voice-over booth project on Newman Street, London. Our rubber floor system greatly reduces the transmission of noise and vibration.
In this video, the jack screws are turned in succession to achieve the desired air gap. The floor system is comprised of low dynamic stiffness natural rubber mounts that are designed to absorb vibration and noise by isolating the floor from the surrounding structure. The floor finish and walls are supported on the floating floor to create a fully isolated box. These are installed after the jacking of the floor, and are included in the design loads for the floating floor.
This video includes a time-lapse capture showing the floor jacking of a free weights area for a gym in Liverpool. Our Sprung floor system greatly reduces the transmission of impact noise through the application of spring isolators.
In this video, the jack screws are turned in succession to achieve the desired are gap. The floor system is comprised of spring mounts that are designed to absorb impact and low frequency vibration and noise, and to isolate the floor from the existing structure below. The floor finish and walls are added after the jacking of the floor, and are included in the design loads for the floor.
This video includes two time-lapse captures showing both the concrete pour and the floor jacking of a free weights area for a gym in Cwmbran, Wales. Our Sprung floor system greatly reduces the transmission of impact noise through the application of spring isolators.
In the video, the reinforcing structure and jacks are seen, but are quickly encased inside 100mm of concrete. Once the concrete has cured, after 2-3 days, the floor is then lifted by adjusting the Mason Floor Jacks. The desired air gap of 50mm was achieved, as per the specification.
Floating Floor Systems
There are a variety of floating floor systems available.
The design and type of the floating floor is determined by the level of required isolation, the supporting structure and any loads on the floor from walls, equipment etc. Mason U.K. have long experience in this field and would be happy to help interpret any requirements or specifications and provide a practical solution.
Construction of a jack-up floating floor
The purpose of a jack-up floating floor is to create a �floating� concrete slab supported at regular intervals by jacks, in order to create an air gap underneath. Our system allows each jack to be adjusted independently, varying the air gap to suit. This also allows the slab to be accurately levelled and lifted to whatever datum or threshold is required. The basic construction process as follows:
1) Each jack has to be placed in the correct position. Following our design, each position is marked o the floor.
2) The floating slab must not touch any of the existing structure. To isolate the edges, mineral wool is placed against all walls, columns etc. the floor will be constructed against this isolating layer.
3) Bond-breaking polythene is laid across the entire floor and up the walls to protect the surface.
4) The jacks are placed onto the polythene and locked into place with reinforcing bar. Reinforcing steel is then laid across the entire area, typically two layers of mesh is required.
5) The concrete is poured to the correct thickness and allowed to cure for 3-4 days or until the minimum required strength has been reached. Each jack has a rubber nipple which protrudes from the concrete. Any required finishing is carried out.
6) The rubber seal is removed from the top of each jack and a bolt inserted. The bolt length is determined by the required air gap. Waist height screwdrivers are used to screw the bolt into each jack, which engages on the rubber element within. As the bolts are wound downwards, the slab begins to lift. The team of workers works their way across the floor in a wave like pattern, gradually lifting the slab to the required height.
7) The floor level is checked at regular intervals across the whole area and individual jacks adjusted as necessary. Once the customer is happy with the floor position, the works are complete and other trades can start work.
Associated Products
MFS Lightweight Floor Spring
MFS datasheet![]() |
Jack-Up LDS Rubber Floating Floors
Small FSN Floating Floor Mount![]() Large FSN Floating Floor Mount![]() Floating floor brochure![]() |
Jack-Up Spring Floating Floors
Spring Mount Floating Floors PDF![]() |
Form Work Floating Floor
EAFM Floor Mounts![]() |
Concrete Floating Floors
Spring Floating Floors PDF![]() Rubber Floating Floors PDF![]() |